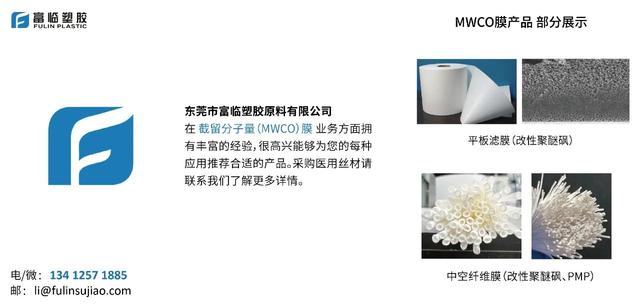
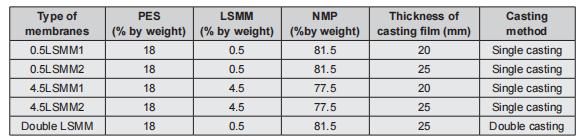
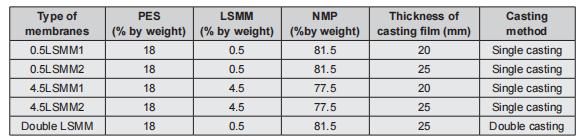






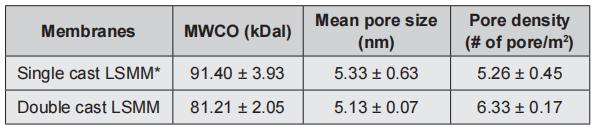
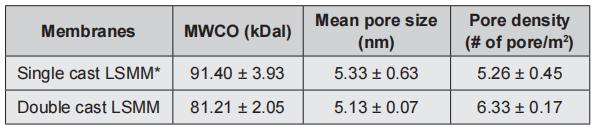
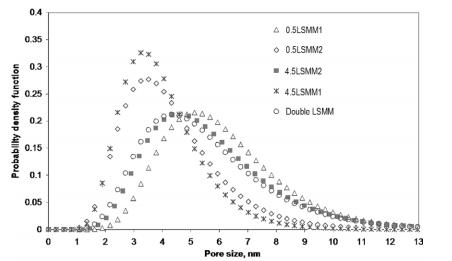
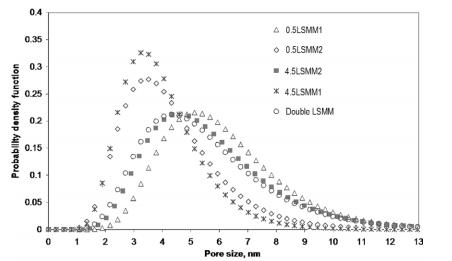
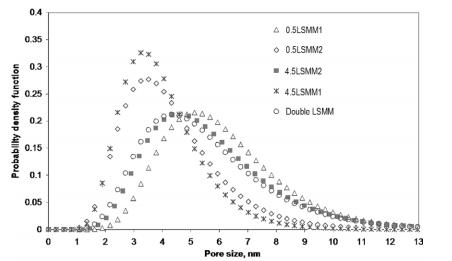
东莞市富临塑胶原料有限公司供应医用植入级医用:可吸收单丝/复丝/聚合物/无纺布、不可吸收单丝/复丝/绳/带/网片
邮:li@fulinsujiao.com
电:134 1257 1885
公司地址:广东省东莞市樟木头镇塑金国际1号楼810
邮:li@fulinsujiao.com
电:134 1257 1885
公司地址:广东省东莞市樟木头镇塑金国际1号楼810
◎欢迎参与讨论,请在这里发表您的看法、交流您的观点。
Powered By Z-BlogPHP 1.7.3
ICP证:湘ICP备2021010693号-4